Evidence of a warped build plate?
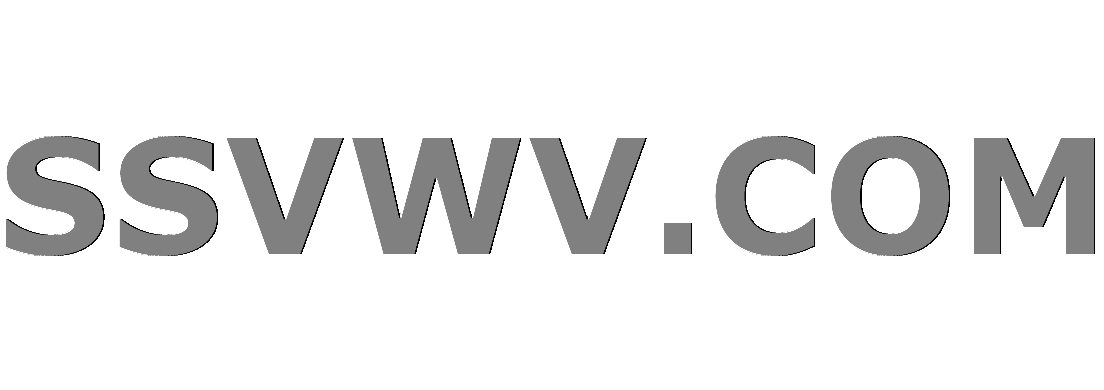
Multi tool use
The first layer is very patchy indeed. I've calibrated the build plate pretty accurately but even if it was a badly calibrated build plate I don't think it would have this effect.
It doesn't seem to have a negative effect on the print.
- Should I be concerned about this?
- Is this due to a the build plate fault?
print-quality heated-bed calibration print-failure
add a comment |
The first layer is very patchy indeed. I've calibrated the build plate pretty accurately but even if it was a badly calibrated build plate I don't think it would have this effect.
It doesn't seem to have a negative effect on the print.
- Should I be concerned about this?
- Is this due to a the build plate fault?
print-quality heated-bed calibration print-failure
That's some strange warping. Usually, glass plates will have a slight U shape when they're warped.
– Sava
Dec 21 '18 at 13:17
It looks like a Buildtak clone
– Trish
Dec 21 '18 at 13:35
add a comment |
The first layer is very patchy indeed. I've calibrated the build plate pretty accurately but even if it was a badly calibrated build plate I don't think it would have this effect.
It doesn't seem to have a negative effect on the print.
- Should I be concerned about this?
- Is this due to a the build plate fault?
print-quality heated-bed calibration print-failure
The first layer is very patchy indeed. I've calibrated the build plate pretty accurately but even if it was a badly calibrated build plate I don't think it would have this effect.
It doesn't seem to have a negative effect on the print.
- Should I be concerned about this?
- Is this due to a the build plate fault?
print-quality heated-bed calibration print-failure
print-quality heated-bed calibration print-failure
edited Dec 21 '18 at 13:55
Trish
4,662938
4,662938
asked Dec 21 '18 at 13:05
BanksySan
1899
1899
That's some strange warping. Usually, glass plates will have a slight U shape when they're warped.
– Sava
Dec 21 '18 at 13:17
It looks like a Buildtak clone
– Trish
Dec 21 '18 at 13:35
add a comment |
That's some strange warping. Usually, glass plates will have a slight U shape when they're warped.
– Sava
Dec 21 '18 at 13:17
It looks like a Buildtak clone
– Trish
Dec 21 '18 at 13:35
That's some strange warping. Usually, glass plates will have a slight U shape when they're warped.
– Sava
Dec 21 '18 at 13:17
That's some strange warping. Usually, glass plates will have a slight U shape when they're warped.
– Sava
Dec 21 '18 at 13:17
It looks like a Buildtak clone
– Trish
Dec 21 '18 at 13:35
It looks like a Buildtak clone
– Trish
Dec 21 '18 at 13:35
add a comment |
2 Answers
2
active
oldest
votes
First things first:
Don't Panic
Your heated bed is made from metal with some sort of Build-Tak-Clone surface. It is not broken from what I can see. Your print is not failed, however, the quality does suffer a little bit.
Your bed does warp a little under heating. That is perfectly normal, and you should actually calibrate your layer thickness against a hot heatbed, not a cold one as metal that is heatbed extends - especially over the heating elements. The main heating element is usually in the center, so it "bulges" a little there, and if the heat has not equalized everywhere, it can show a dimple around it. So it warps slightly. The extent of the warping is determined by a couple factors, but from what your print looks like, it is not in a worrisome amount - the second and third layers will even it out.
I can't tell how much time passed between reaching the print temperature of the bed and the start of the print, but you might want to make sure the heating behavior heats the bed first and the hotend second, allowing the heat energy in the bed to spread more evenly. A tiny G4 P20000 ; wait 20 seconds
(see here)` in the pre-print code, before cleaning & priming the nozzle might also help.
You can try to get more even first layers by positioning the parts in areas that do not suffer from warping.
As Tom mentioned, you might get better base layers if you increase the first layer thickness. I usually print with about 0.15 to 0.2 mm for the first layer, regardless of the following layer thickness to even out small miscalibrations and unevenness in the heating.
Good piont about calibrarinbg against hot parts!
– BanksySan
Dec 21 '18 at 14:39
add a comment |
It looks like your first layer is way too close to the bed. The printer is trying to squash the plastic down very thinly, resulting in inconsistent extrusion. You will likely see better results if you move the nozzle away from the bed a little bit. Increasing the thickness of the first layer might help as well (this is a setting in your slicer).
Keep in mind that if you're trying to print (e.g.) a first layer with a thickness of 0.05mm then a 0.025mm variation in the height of the build plate will result in very strong variation in the thickness of the extrusion on the first layer; in some places it will only be half as thick as in other places. If instead you used a 0.2mm first layer, then the 0.025mm variation barely makes a difference.
If that were the case wouldn't I see a different pattern? The calibration screws are triangular with one at the front and one at each far corner.
– BanksySan
Dec 21 '18 at 16:48
The pattern is determined by tiny variations in the surface of the build plate. It doesn't have anything to do with the way it's mounted.
– Tom van der Zanden
Dec 21 '18 at 21:31
the instructions said to use a piece of printer paper for the final measurement (first measurement was 1mm). I favoured the point before the paper snagged rather than after.
– BanksySan
Dec 22 '18 at 1:18
@BanksySan that... actually is too close: you want to use the point where the paper binds on pull or starts to bend if you push.
– Trish
Dec 22 '18 at 10:14
1
@BanksySan that is babystepping. babystepping is "adjust the general layer height by a tiny ammount" not "Fix a skewed build platform"
– Trish
Dec 22 '18 at 13:54
|
show 4 more comments
Your Answer
StackExchange.ifUsing("editor", function () {
return StackExchange.using("mathjaxEditing", function () {
StackExchange.MarkdownEditor.creationCallbacks.add(function (editor, postfix) {
StackExchange.mathjaxEditing.prepareWmdForMathJax(editor, postfix, [["$", "$"], ["\\(","\\)"]]);
});
});
}, "mathjax-editing");
StackExchange.ready(function() {
var channelOptions = {
tags: "".split(" "),
id: "640"
};
initTagRenderer("".split(" "), "".split(" "), channelOptions);
StackExchange.using("externalEditor", function() {
// Have to fire editor after snippets, if snippets enabled
if (StackExchange.settings.snippets.snippetsEnabled) {
StackExchange.using("snippets", function() {
createEditor();
});
}
else {
createEditor();
}
});
function createEditor() {
StackExchange.prepareEditor({
heartbeatType: 'answer',
autoActivateHeartbeat: false,
convertImagesToLinks: false,
noModals: true,
showLowRepImageUploadWarning: true,
reputationToPostImages: null,
bindNavPrevention: true,
postfix: "",
imageUploader: {
brandingHtml: "Powered by u003ca class="icon-imgur-white" href="https://imgur.com/"u003eu003c/au003e",
contentPolicyHtml: "User contributions licensed under u003ca href="https://creativecommons.org/licenses/by-sa/3.0/"u003ecc by-sa 3.0 with attribution requiredu003c/au003e u003ca href="https://stackoverflow.com/legal/content-policy"u003e(content policy)u003c/au003e",
allowUrls: true
},
noCode: true, onDemand: true,
discardSelector: ".discard-answer"
,immediatelyShowMarkdownHelp:true
});
}
});
Sign up or log in
StackExchange.ready(function () {
StackExchange.helpers.onClickDraftSave('#login-link');
});
Sign up using Google
Sign up using Facebook
Sign up using Email and Password
Post as a guest
Required, but never shown
StackExchange.ready(
function () {
StackExchange.openid.initPostLogin('.new-post-login', 'https%3a%2f%2f3dprinting.stackexchange.com%2fquestions%2f7740%2fevidence-of-a-warped-build-plate%23new-answer', 'question_page');
}
);
Post as a guest
Required, but never shown
2 Answers
2
active
oldest
votes
2 Answers
2
active
oldest
votes
active
oldest
votes
active
oldest
votes
First things first:
Don't Panic
Your heated bed is made from metal with some sort of Build-Tak-Clone surface. It is not broken from what I can see. Your print is not failed, however, the quality does suffer a little bit.
Your bed does warp a little under heating. That is perfectly normal, and you should actually calibrate your layer thickness against a hot heatbed, not a cold one as metal that is heatbed extends - especially over the heating elements. The main heating element is usually in the center, so it "bulges" a little there, and if the heat has not equalized everywhere, it can show a dimple around it. So it warps slightly. The extent of the warping is determined by a couple factors, but from what your print looks like, it is not in a worrisome amount - the second and third layers will even it out.
I can't tell how much time passed between reaching the print temperature of the bed and the start of the print, but you might want to make sure the heating behavior heats the bed first and the hotend second, allowing the heat energy in the bed to spread more evenly. A tiny G4 P20000 ; wait 20 seconds
(see here)` in the pre-print code, before cleaning & priming the nozzle might also help.
You can try to get more even first layers by positioning the parts in areas that do not suffer from warping.
As Tom mentioned, you might get better base layers if you increase the first layer thickness. I usually print with about 0.15 to 0.2 mm for the first layer, regardless of the following layer thickness to even out small miscalibrations and unevenness in the heating.
Good piont about calibrarinbg against hot parts!
– BanksySan
Dec 21 '18 at 14:39
add a comment |
First things first:
Don't Panic
Your heated bed is made from metal with some sort of Build-Tak-Clone surface. It is not broken from what I can see. Your print is not failed, however, the quality does suffer a little bit.
Your bed does warp a little under heating. That is perfectly normal, and you should actually calibrate your layer thickness against a hot heatbed, not a cold one as metal that is heatbed extends - especially over the heating elements. The main heating element is usually in the center, so it "bulges" a little there, and if the heat has not equalized everywhere, it can show a dimple around it. So it warps slightly. The extent of the warping is determined by a couple factors, but from what your print looks like, it is not in a worrisome amount - the second and third layers will even it out.
I can't tell how much time passed between reaching the print temperature of the bed and the start of the print, but you might want to make sure the heating behavior heats the bed first and the hotend second, allowing the heat energy in the bed to spread more evenly. A tiny G4 P20000 ; wait 20 seconds
(see here)` in the pre-print code, before cleaning & priming the nozzle might also help.
You can try to get more even first layers by positioning the parts in areas that do not suffer from warping.
As Tom mentioned, you might get better base layers if you increase the first layer thickness. I usually print with about 0.15 to 0.2 mm for the first layer, regardless of the following layer thickness to even out small miscalibrations and unevenness in the heating.
Good piont about calibrarinbg against hot parts!
– BanksySan
Dec 21 '18 at 14:39
add a comment |
First things first:
Don't Panic
Your heated bed is made from metal with some sort of Build-Tak-Clone surface. It is not broken from what I can see. Your print is not failed, however, the quality does suffer a little bit.
Your bed does warp a little under heating. That is perfectly normal, and you should actually calibrate your layer thickness against a hot heatbed, not a cold one as metal that is heatbed extends - especially over the heating elements. The main heating element is usually in the center, so it "bulges" a little there, and if the heat has not equalized everywhere, it can show a dimple around it. So it warps slightly. The extent of the warping is determined by a couple factors, but from what your print looks like, it is not in a worrisome amount - the second and third layers will even it out.
I can't tell how much time passed between reaching the print temperature of the bed and the start of the print, but you might want to make sure the heating behavior heats the bed first and the hotend second, allowing the heat energy in the bed to spread more evenly. A tiny G4 P20000 ; wait 20 seconds
(see here)` in the pre-print code, before cleaning & priming the nozzle might also help.
You can try to get more even first layers by positioning the parts in areas that do not suffer from warping.
As Tom mentioned, you might get better base layers if you increase the first layer thickness. I usually print with about 0.15 to 0.2 mm for the first layer, regardless of the following layer thickness to even out small miscalibrations and unevenness in the heating.
First things first:
Don't Panic
Your heated bed is made from metal with some sort of Build-Tak-Clone surface. It is not broken from what I can see. Your print is not failed, however, the quality does suffer a little bit.
Your bed does warp a little under heating. That is perfectly normal, and you should actually calibrate your layer thickness against a hot heatbed, not a cold one as metal that is heatbed extends - especially over the heating elements. The main heating element is usually in the center, so it "bulges" a little there, and if the heat has not equalized everywhere, it can show a dimple around it. So it warps slightly. The extent of the warping is determined by a couple factors, but from what your print looks like, it is not in a worrisome amount - the second and third layers will even it out.
I can't tell how much time passed between reaching the print temperature of the bed and the start of the print, but you might want to make sure the heating behavior heats the bed first and the hotend second, allowing the heat energy in the bed to spread more evenly. A tiny G4 P20000 ; wait 20 seconds
(see here)` in the pre-print code, before cleaning & priming the nozzle might also help.
You can try to get more even first layers by positioning the parts in areas that do not suffer from warping.
As Tom mentioned, you might get better base layers if you increase the first layer thickness. I usually print with about 0.15 to 0.2 mm for the first layer, regardless of the following layer thickness to even out small miscalibrations and unevenness in the heating.
edited Dec 21 '18 at 15:38
answered Dec 21 '18 at 14:09
Trish
4,662938
4,662938
Good piont about calibrarinbg against hot parts!
– BanksySan
Dec 21 '18 at 14:39
add a comment |
Good piont about calibrarinbg against hot parts!
– BanksySan
Dec 21 '18 at 14:39
Good piont about calibrarinbg against hot parts!
– BanksySan
Dec 21 '18 at 14:39
Good piont about calibrarinbg against hot parts!
– BanksySan
Dec 21 '18 at 14:39
add a comment |
It looks like your first layer is way too close to the bed. The printer is trying to squash the plastic down very thinly, resulting in inconsistent extrusion. You will likely see better results if you move the nozzle away from the bed a little bit. Increasing the thickness of the first layer might help as well (this is a setting in your slicer).
Keep in mind that if you're trying to print (e.g.) a first layer with a thickness of 0.05mm then a 0.025mm variation in the height of the build plate will result in very strong variation in the thickness of the extrusion on the first layer; in some places it will only be half as thick as in other places. If instead you used a 0.2mm first layer, then the 0.025mm variation barely makes a difference.
If that were the case wouldn't I see a different pattern? The calibration screws are triangular with one at the front and one at each far corner.
– BanksySan
Dec 21 '18 at 16:48
The pattern is determined by tiny variations in the surface of the build plate. It doesn't have anything to do with the way it's mounted.
– Tom van der Zanden
Dec 21 '18 at 21:31
the instructions said to use a piece of printer paper for the final measurement (first measurement was 1mm). I favoured the point before the paper snagged rather than after.
– BanksySan
Dec 22 '18 at 1:18
@BanksySan that... actually is too close: you want to use the point where the paper binds on pull or starts to bend if you push.
– Trish
Dec 22 '18 at 10:14
1
@BanksySan that is babystepping. babystepping is "adjust the general layer height by a tiny ammount" not "Fix a skewed build platform"
– Trish
Dec 22 '18 at 13:54
|
show 4 more comments
It looks like your first layer is way too close to the bed. The printer is trying to squash the plastic down very thinly, resulting in inconsistent extrusion. You will likely see better results if you move the nozzle away from the bed a little bit. Increasing the thickness of the first layer might help as well (this is a setting in your slicer).
Keep in mind that if you're trying to print (e.g.) a first layer with a thickness of 0.05mm then a 0.025mm variation in the height of the build plate will result in very strong variation in the thickness of the extrusion on the first layer; in some places it will only be half as thick as in other places. If instead you used a 0.2mm first layer, then the 0.025mm variation barely makes a difference.
If that were the case wouldn't I see a different pattern? The calibration screws are triangular with one at the front and one at each far corner.
– BanksySan
Dec 21 '18 at 16:48
The pattern is determined by tiny variations in the surface of the build plate. It doesn't have anything to do with the way it's mounted.
– Tom van der Zanden
Dec 21 '18 at 21:31
the instructions said to use a piece of printer paper for the final measurement (first measurement was 1mm). I favoured the point before the paper snagged rather than after.
– BanksySan
Dec 22 '18 at 1:18
@BanksySan that... actually is too close: you want to use the point where the paper binds on pull or starts to bend if you push.
– Trish
Dec 22 '18 at 10:14
1
@BanksySan that is babystepping. babystepping is "adjust the general layer height by a tiny ammount" not "Fix a skewed build platform"
– Trish
Dec 22 '18 at 13:54
|
show 4 more comments
It looks like your first layer is way too close to the bed. The printer is trying to squash the plastic down very thinly, resulting in inconsistent extrusion. You will likely see better results if you move the nozzle away from the bed a little bit. Increasing the thickness of the first layer might help as well (this is a setting in your slicer).
Keep in mind that if you're trying to print (e.g.) a first layer with a thickness of 0.05mm then a 0.025mm variation in the height of the build plate will result in very strong variation in the thickness of the extrusion on the first layer; in some places it will only be half as thick as in other places. If instead you used a 0.2mm first layer, then the 0.025mm variation barely makes a difference.
It looks like your first layer is way too close to the bed. The printer is trying to squash the plastic down very thinly, resulting in inconsistent extrusion. You will likely see better results if you move the nozzle away from the bed a little bit. Increasing the thickness of the first layer might help as well (this is a setting in your slicer).
Keep in mind that if you're trying to print (e.g.) a first layer with a thickness of 0.05mm then a 0.025mm variation in the height of the build plate will result in very strong variation in the thickness of the extrusion on the first layer; in some places it will only be half as thick as in other places. If instead you used a 0.2mm first layer, then the 0.025mm variation barely makes a difference.
answered Dec 21 '18 at 14:37
Tom van der Zanden
11k11745
11k11745
If that were the case wouldn't I see a different pattern? The calibration screws are triangular with one at the front and one at each far corner.
– BanksySan
Dec 21 '18 at 16:48
The pattern is determined by tiny variations in the surface of the build plate. It doesn't have anything to do with the way it's mounted.
– Tom van der Zanden
Dec 21 '18 at 21:31
the instructions said to use a piece of printer paper for the final measurement (first measurement was 1mm). I favoured the point before the paper snagged rather than after.
– BanksySan
Dec 22 '18 at 1:18
@BanksySan that... actually is too close: you want to use the point where the paper binds on pull or starts to bend if you push.
– Trish
Dec 22 '18 at 10:14
1
@BanksySan that is babystepping. babystepping is "adjust the general layer height by a tiny ammount" not "Fix a skewed build platform"
– Trish
Dec 22 '18 at 13:54
|
show 4 more comments
If that were the case wouldn't I see a different pattern? The calibration screws are triangular with one at the front and one at each far corner.
– BanksySan
Dec 21 '18 at 16:48
The pattern is determined by tiny variations in the surface of the build plate. It doesn't have anything to do with the way it's mounted.
– Tom van der Zanden
Dec 21 '18 at 21:31
the instructions said to use a piece of printer paper for the final measurement (first measurement was 1mm). I favoured the point before the paper snagged rather than after.
– BanksySan
Dec 22 '18 at 1:18
@BanksySan that... actually is too close: you want to use the point where the paper binds on pull or starts to bend if you push.
– Trish
Dec 22 '18 at 10:14
1
@BanksySan that is babystepping. babystepping is "adjust the general layer height by a tiny ammount" not "Fix a skewed build platform"
– Trish
Dec 22 '18 at 13:54
If that were the case wouldn't I see a different pattern? The calibration screws are triangular with one at the front and one at each far corner.
– BanksySan
Dec 21 '18 at 16:48
If that were the case wouldn't I see a different pattern? The calibration screws are triangular with one at the front and one at each far corner.
– BanksySan
Dec 21 '18 at 16:48
The pattern is determined by tiny variations in the surface of the build plate. It doesn't have anything to do with the way it's mounted.
– Tom van der Zanden
Dec 21 '18 at 21:31
The pattern is determined by tiny variations in the surface of the build plate. It doesn't have anything to do with the way it's mounted.
– Tom van der Zanden
Dec 21 '18 at 21:31
the instructions said to use a piece of printer paper for the final measurement (first measurement was 1mm). I favoured the point before the paper snagged rather than after.
– BanksySan
Dec 22 '18 at 1:18
the instructions said to use a piece of printer paper for the final measurement (first measurement was 1mm). I favoured the point before the paper snagged rather than after.
– BanksySan
Dec 22 '18 at 1:18
@BanksySan that... actually is too close: you want to use the point where the paper binds on pull or starts to bend if you push.
– Trish
Dec 22 '18 at 10:14
@BanksySan that... actually is too close: you want to use the point where the paper binds on pull or starts to bend if you push.
– Trish
Dec 22 '18 at 10:14
1
1
@BanksySan that is babystepping. babystepping is "adjust the general layer height by a tiny ammount" not "Fix a skewed build platform"
– Trish
Dec 22 '18 at 13:54
@BanksySan that is babystepping. babystepping is "adjust the general layer height by a tiny ammount" not "Fix a skewed build platform"
– Trish
Dec 22 '18 at 13:54
|
show 4 more comments
Thanks for contributing an answer to 3D Printing Stack Exchange!
- Please be sure to answer the question. Provide details and share your research!
But avoid …
- Asking for help, clarification, or responding to other answers.
- Making statements based on opinion; back them up with references or personal experience.
Use MathJax to format equations. MathJax reference.
To learn more, see our tips on writing great answers.
Some of your past answers have not been well-received, and you're in danger of being blocked from answering.
Please pay close attention to the following guidance:
- Please be sure to answer the question. Provide details and share your research!
But avoid …
- Asking for help, clarification, or responding to other answers.
- Making statements based on opinion; back them up with references or personal experience.
To learn more, see our tips on writing great answers.
Sign up or log in
StackExchange.ready(function () {
StackExchange.helpers.onClickDraftSave('#login-link');
});
Sign up using Google
Sign up using Facebook
Sign up using Email and Password
Post as a guest
Required, but never shown
StackExchange.ready(
function () {
StackExchange.openid.initPostLogin('.new-post-login', 'https%3a%2f%2f3dprinting.stackexchange.com%2fquestions%2f7740%2fevidence-of-a-warped-build-plate%23new-answer', 'question_page');
}
);
Post as a guest
Required, but never shown
Sign up or log in
StackExchange.ready(function () {
StackExchange.helpers.onClickDraftSave('#login-link');
});
Sign up using Google
Sign up using Facebook
Sign up using Email and Password
Post as a guest
Required, but never shown
Sign up or log in
StackExchange.ready(function () {
StackExchange.helpers.onClickDraftSave('#login-link');
});
Sign up using Google
Sign up using Facebook
Sign up using Email and Password
Post as a guest
Required, but never shown
Sign up or log in
StackExchange.ready(function () {
StackExchange.helpers.onClickDraftSave('#login-link');
});
Sign up using Google
Sign up using Facebook
Sign up using Email and Password
Sign up using Google
Sign up using Facebook
Sign up using Email and Password
Post as a guest
Required, but never shown
Required, but never shown
Required, but never shown
Required, but never shown
Required, but never shown
Required, but never shown
Required, but never shown
Required, but never shown
Required, but never shown
Srx,wgVtgQABHpq,4M4Ww,9mj7F,H,l
That's some strange warping. Usually, glass plates will have a slight U shape when they're warped.
– Sava
Dec 21 '18 at 13:17
It looks like a Buildtak clone
– Trish
Dec 21 '18 at 13:35